A time of peace, a season of wonder and joy... We wish you all the best during the holidays and through the coming year, from your friends at Swanson Flo.

The Swanson Flo Blog is dedicated to provide educational and new product information on process control instrumentation, control valves, and valve automation. For more information on these products, visit SwansonFlo.com or call 800-288-7926.
Brewery Valve Application Guide
![]() |
Download the Brewery Valve Application Guide Here |
Many types of valves are commonly used in a brewery to regulate the flow of fluids throughout process pipes in a plant.
One type is the diaphragm valve, in which a soft diaphragm is pushed against a bell-shaped feature using a mechanical screw . This mechanism allows gas or liquid flow to be controlled within the valve’s total variability, but the flow pressure tolerances are fairly tight.
The butterfly valve is the next most commonly used valve in breweries due to its compact design and wide pressure and flow tolerances. It consists of a metal disc which rotates within the body of the valve and closes against a rubber seal. Its flow-through design makes it easy to clean.
The Brewery Valve Application Guide, located on Swanson Flo web site, provides a quick reference on the various processes involved in brewing and what type of valves are used for those processes.
Changing VR Actuator Orientation on Valtek Rotary Valves, including Valdisk, Shearstream and MaxFlo
The Valtek VR rotary cylinder actuator is a high pressure, compact actuator with high torque and pneumatic stiffness for excellent throttling capabilities. The standard splined shaft connection eliminates backlash for precise control. This video shows how to change the orientation on a Valtek Rotary Valves including Valdisk, Shearstream and MaxFlo products.
For more infomration on Valtek Control Valves, contact Swanson Flo by calling 800-288-7926 or by visiting https://swansonflo.com.
Posted by
Swanson Flo
Labels:
actuator,
Control Valve,
Flowserve,
Illinois,
Indiana,
Iowa,
Michigan,
Minnesota,
Montana,
Nebraska,
North Dakota,
South Dakota,
Valtek,
Wisconsin,
Wyoming
Swanson Flo Salutes Our Veterans
Veterans Day is set aside to honor the men and women who have sacrificed so much in order to serve in the armed forces of the United States.
Veterans Day celebrates and thanks all United States military veterans, alive or dead, and honors the sacrifices that they have made. Our Veterans are our neighbors, friends, family, and co-workers. They took an oath to defend the United States and our Constitution, from all enemies, foreign and domestic. We must never forget their bravery, service, and sacrifice.
Originally called Armistice Day because of the November 11 Armistice that ended World War I, its name was officially changed in the United States in 1954 to Veterans Day to include Veterans of all wars.
Through the observance of Veterans Day, we remind ourselves of our Veterans patriotism, love of country and willingness to serve and sacrifice for the common good.
Swanson Flo celebrates and honors America's veterans.
Posted by
Swanson Flo
Electric Valve Actuation
![]() |
Electric Valve Actuator in Service (Limitorque) |
Electric Valve Actuation Advantages
- Electric power is relatively inexpensive, easy to manage, and normally available to most industrial sites. The capital cost of electric actuators is typically cheaper per equivalent unit of torque/thrust output. They’re also cleaner and safer to operate.
- Electric actuators can provide superior positioning accuracy for control or modulating valve functions, which can include provisions for a high degree of process monitoring, data logging and information feedback.
- All necessary control functions are integral to electric actuators, reducing capital costs.
- Electric actuators significantly reduce control wiring costs by enabling distributed control. They simplify control logic by integrating control commands and feedback into customer SCADA or DCS systems. (Traditional electromechanical control systems require a dedicated wire for each command and feedback signal, leading to cable bundles with seven or more cores as minimum for each actuator. By contrast, a typical bus system can use one twisted pair wire in a daisy chain configuration to carry all required input and output signals.)
- As torque and thrust requirements increase, electric actuators weigh less and have smaller footprints compared to pneumatic actuators.
- Electric actuators may be combined with external gearboxes to produce extremely high output thrust and torque values.
Electric Valve Actuation Disadvantages
- With the exception of a few specific configurations, electric actuators can’t guarantee a fail-safe stroke but will “fail in the last position.” (Fail-safe stroke refers to an actuator’s ability to move a valve to a predefined safe position when power fails).
- Electric actuators have more complex and sensitive components than the mechanical parts used in other types of actuators. Electronic technology also requires periodic refreshing to keep pace with component changes and improvements.
- Beyond a certain size/torque range, electric actuators are less cost-effective and generally have limitations in operating speed when compared to pneumatic and hydraulic actuators.
- In hazardous areas with potential exposure to explosive process media, electric actuators require more specific certifications and construction features to be considered safe for use.
Recommended applications for electric actuation.
Electric actuation is the first choice for most oil and gas applications. They’re ideal for general process valve automation, non-critical applications, and light-duty modulating applications (generally up to 1200 starts per hour), although some can modulate continuously up to 3600 starts per hour.
For more information about electric valve actuation, contact Swanson Flo. Call them at 800-288-7926 or visit their web site at https://swansonflo.com.
Reprinted with permission from Flowserve Limitorque.
Posted by
Swanson Flo
Labels:
electric valve actuation,
Illinois,
Indiana,
Iowa,
Limitorque,
Michigan,
Minnesota,
Montana,
Nebraska,
North Dakota,
South Dakota,
Wisconsin,
Wyoming
Dual-Seal Trunnion Mounted Ball Valves Offer Twice the Life for Pipeline, Petrochemical, and Process Industries
![]() |
WOM trunnion mounted ball valves in service. |
![]() |
The only trunnion mounted ball valve with two independent seats. |
the secondary seat.
WOM’s Dual Seal Ball Valve typically comes with two seats upstream and two seats downstream of the ball. But it can be configured to have the outer seat on the downstream side modified to act as a Third seal. The third seal will provide one more seal on the downstream side of the valve. The valve is still bi-direction, even with the third seal option.
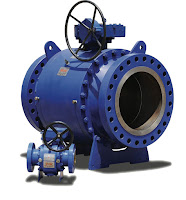
Redundant sealing technology, the third seal, and being able to control the direction of the thermal expansion pressure makes the Dual-Seal ball valve unsurpassed in real life performance. This combination of seats gives you a valve that will outlast typical ball or gate valves. It will lower your operational costs, add safety, and increase reliability.
For more infomration on WOM trunnion mount ball valves, contact Swanson Flo. Call them at 800-288-7926 of visit https://swansonflo.com.
Posted by
Swanson Flo
Labels:
Illinois,
Indiana,
Iowa,
Michigan,
Minnesota,
Montana,
Nebraska,
North Dakota,
South Dakota,
trunnion mount ball valve,
Wisconsin,
WOM,
Worldwide Oilfield Machine,
Wyoming
Accurate Dosing of Corrosion Inhibitors Greatly Improves Corrosion Prevention and Extends Pipeline Life
Accurate dosing of corrosion inhibitors in industrial applications, especially in the chemical, process and oil and gas industry can be a real challenge. These industries cope with demanding environmental and process conditions in production and operation. In oil and gas, it is common that wells produce other products that are likely to cause corrosion, such as water and carbon dioxide. Pipelines are required to transport oil and gas products from the well, sometimes over long distances. Even though they are designed to last for decades, corrosion processes are responsible for degradation and significant losses. It is clear that the best way to combat corrosion economically is through prevention using chemical inhibitors.
A corrosion inhibitor system will add small concentrations of (bio)chemicals into the process which form a film on the interior surface of the pipe or vessel, preventing corrosive attack. The effectiveness of an inhibitor system greatly depends on the correct injection amount, and can be influenced by the environmental and process conditions; so accuracy is crucial here. A properly applied chemical corrosion inhibitor system is very effective in lowering corrosion rates, with the potential to reduce corrosion rates up to 99%.
The key in determining the overall rate of corrosion over the life of a pipeline is determined by the proportion of time for which the corrosion inhibitor is available, and the correct concentration. In order to accurately assess the availability of corrosion inhibitor, it is necessary to have some means of accurately measuring the dosage of inhibitor being injected.
Using a low flow control system containing a mass flow controller (MFC) allows for very accurate corrosion inhibitor dosing. High accuracy and high turndown ratio is achieved based on pure mass flow measurement with this type of flow meter. A device such as the Bronkhorst (mini) CORI-FLOW mass flow controller can directly control valves and pumps via it's on-board PID controller, and be further optimized with ancillary PLC and HMI controls, extending both performance and flexibility.
The application of chemical corrosion inhibitors can significantly reduce the rate of corrosion and using a dosing system with an integrated MFC (such as the Bronkhorst (mini) CORI-FLOW) enables real-time monitoring, control and logging of injection rates. This allows online checking of flow rates and instantaneous re-setting of the required flow rate. Asset management and preventive maintenance is supported with several active diagnostics.
For more information about mass flow controllers used in chemical dosing applications, contact Swanson Flo by calling 800-288-7926 or visit https://swansonflo.com.
A corrosion inhibitor system will add small concentrations of (bio)chemicals into the process which form a film on the interior surface of the pipe or vessel, preventing corrosive attack. The effectiveness of an inhibitor system greatly depends on the correct injection amount, and can be influenced by the environmental and process conditions; so accuracy is crucial here. A properly applied chemical corrosion inhibitor system is very effective in lowering corrosion rates, with the potential to reduce corrosion rates up to 99%.
The key in determining the overall rate of corrosion over the life of a pipeline is determined by the proportion of time for which the corrosion inhibitor is available, and the correct concentration. In order to accurately assess the availability of corrosion inhibitor, it is necessary to have some means of accurately measuring the dosage of inhibitor being injected.

The application of chemical corrosion inhibitors can significantly reduce the rate of corrosion and using a dosing system with an integrated MFC (such as the Bronkhorst (mini) CORI-FLOW) enables real-time monitoring, control and logging of injection rates. This allows online checking of flow rates and instantaneous re-setting of the required flow rate. Asset management and preventive maintenance is supported with several active diagnostics.
For more information about mass flow controllers used in chemical dosing applications, contact Swanson Flo by calling 800-288-7926 or visit https://swansonflo.com.
Posted by
Swanson Flo
Labels:
Bronkhorst,
chemical dosing,
corrosion,
Illinois,
Indiana,
Iowa,
mass flow controller,
MFC,
Michigan,
Minnesota,
Montana,
Nebraska,
North Dakota,
pipe systems,
South Dakota,
Wisconsin,
Wyoming
The ASCO FasN Connection System for the Series 212 Composite Valve: A Tutorial
The ASCO Series 212 composite valve is ideal for use in mid-size reverse osmosis water purification systems used for conditioning and distribution in commercial/ industrial markets. The valves are available in 3/8", 1/2", 3/4", and 1" pipe sizes and handles pressure up to 150 PSI at temperatures up to 180° F.
The ASCO FasN connection system makes installing and servicing the series 212 extremely easy. The video above is a tutorial on how to install the series 212 using the ASCO FasN system for all three types of connections, namely NPT thread connection, turn and lock, and solvent bond.
For more information, contact Swanson Flo by calling 800-288-7926 or visit their web site at https://swansonflo.com.
Foxboro Schneider Electric Vortex Flow Meters
The Foxboro® intelligent, high performance vortex flowmeter transmits a 4-20 mA or digital multi-drop, and a pulse output signal (as applicable) using HART communication protocol for remote configuration, calibration, and monitoring.
Foxboro vortex flow meters have unique vortex sensing with a lifetime warranty; patented algorithms that improve performance in real-world applications; a broad offering of sizes, materials, and end connections, with the widest flow range available today; ease of configuration using FDT technology, and no moving parts ensures low operating and maintenance costs. They are ideal for applications requiring accuracy for totalizing and batching; utility metering of fluids in the process industries; fuel, air, steam, or gas metering for the measurement of energy in any high use application; or stability and repeatability for process control.
The Foxboro vortex flowmeter is perfect for applications within the upstream and downstream Oil & Gas industries, specifically on high pressure pipeline applications for both gases (and vapors) and liquids.
For more infomration, contact Swanson Flo by calling 800-288-7926 or by visiting https://swansonflo.com.
Posted by
Swanson Flo
Labels:
Foxboro,
Illinois,
Indiana,
Iowa,
Michigan,
Minnesota,
Montana,
Nebraska,
North Dakota,
Schneider Electric,
South Dakota,
vortex flow meter,
Wisconsin,
Wyoming
Patented Pressure Gauge Technology Eliminates Need for Liquid Fills
![]() |
Pulsations caused by compressors and other machinery. Patented technology by Ashcroft dampen pulsations without the cost and hassle of liquid-fill. |
In response, Ashcroft developed their patented PLUS!™ Performance technology. Gauges with PLUS!™ Performance employ a unique cartridge that surrounds the pinion with an engineered dampening medium. This viscous compound encapsulates and stabilizes the pinion in order to restrict the overactive pointer motion due to vibration. A throttle screw helps to neutralize pulsation by restricting the flow rate of the pressure medium into the Bourdon tube.
![]() |
Pinion is stabilized by a cartridge with viscous compound. |
For more information, contact Swanson Flo by calling 800-288-7926 or visit their web site at https://swansonflo.com.
Posted by
Swanson Flo
Labels:
Ashcroft,
Illinois,
Indiana,
Iowa,
Michigan,
Minnesota,
Montana,
Nebraska,
North Dakota,
pressure gauge,
South Dakota,
Wisconsin,
Wyoming
The Valtek® Mark Eight™ Y-Pattern Control Valve
![]() |
The Valtek Mark Eight Control Valve Features (Click for larger view) |
Because of its nearly straight-through flow passage, the “Y” style body is less flow restrictive than a normal globe-style body. This permits less pressure to be converted into velocity as the fluid passes through the seat, resulting in a lower valve recovery factor and higher capacity.
Mark Eight’s straight-through design generates less valve and piping turbulence which significantly reduces harmful noise and vibration levels.
Posted by
Swanson Flo
Labels:
Control Valve,
Illinois,
Indiana,
Iowa,
Mark Eight,
Michigan,
Minnesota,
Montana,
Nebraska,
North Dakota,
South Dakota,
Valtek,
Wisconsin,
Wyoming
Applying Gas Pipeline Block Station Valves
A block valve is used on gas transmission systems to isolate a segment of the main gas pipeline for inspection and maintenance, or for shutdown in the case of a natural disaster or pipeline damage.
The block valve is typically a full-bore, soft seated ball valve to allow for scraping. However, this type of valve cannot be opened against full differential pressure without damage to the valve seats. Therefore, a bypass system is installed around the block valve, and used to balance the pipeline pressure prior to opening. Plug valves should be used in the bypass as they are capable of opening and throttling against full differential pressure without damage.
The Requirement of a Bypass
Let's see what would happen if the block valve, which is a soft seated ball valve, was operated against full differential pressure. As it is initially opened the huge pressure drop across the valve generates high velocity flow carrying fine dust, rust, or scale particles in close proximity of the valve seats. This results in seat damage and a block valve that cannot seal bubble tight once closed.
The Bypass Valve Sequence
To avoid this, a bypass system is utilized to balance the pressure either side of the block valve prior to opening it. With the vent valve closed, bypass valve 1 is opened allowing pressure into the bypass. In this case, a plug valve should be used, as it can be opened against full differential pressure without seat damage. Now bypass valve 2 is slowly opened, gradually building pressure in the downstream section until the pressure either side of the block valve is equalized. A plug valve is also used here capable of throttling the flow without seat damaged. With the pressure now equalized the block valve can be opened safely without the risk of seat damage. The two bypass valves have now done their job and can be closed providing bubble tight shutoff against the main pipeline.
Venting a Pipeline Section
Block stations are also used to vent sections of the pipeline into the atmosphere. This operation would start with all valves in the closed position. Bypass valve 1 is then opened allowing pressure into the bypass station. The vent valve is now slowly opened to release the pipeline pressure. Once again, this is a demanding application opening against full differential pressure, hence a plug valve is used to ensure bubble tight isolation to the atmosphere once closed.
For more information, contact Swanson Flo by visiting https://swansonflow.com or by calling 800-288-7926.
Posted by
Swanson Flo
Labels:
ball valve,
Flowserve,
Illinois,
Indiana,
Iowa,
Michigan,
Minnesota,
Montana,
Nebraska,
North Dakota,
pipeline,
plug valve,
South Dakota,
Wisconsin,
Wyoming
US Power Grids, Oil and Gas Industries, and Risk of Hacking
A report released in June, from the security firm Dragos, describes a worrisome development by a hacker group named, “Xenotime” and at least two dangerous oil and gas intrusions and ongoing reconnaissance on United States power grids.
Multiple ICS (Industrial Control Sectors) sectors now face the XENOTIME threat; this means individual verticals – such as oil and gas, manufacturing, or electric – cannot ignore threats to other ICS entities because they are not specifically targeted.
The Dragos researchers have termed this threat proliferation as the world’s most dangerous cyberthreat since an event in 2017 where Xenotime had caused a serious operational outage at a crucial site in the Middle East.
The fact that concerns cybersecurity experts the most is that this hacking attack was a malware that chose to target the facility safety processes (SIS – safety instrumentation system).
For example, when temperatures in a reactor increase to an unsafe level, an SIS will automatically start a cooling process or immediately close a valve to prevent a safety accident. The SIS safety stems are both hardware and software that combine to protect facilities from life threatening accidents.
At this point, no one is sure who is behind Xenotime. Russia has been connected to one of the critical infrastructure attacks in the Ukraine. That attack was viewed to be the first hacker related power grid outage.
This is a “Cause for Concern” post that was published by Dragos on June 14, 2019.
“While none of the electric utility targeting events has resulted in a known, successful intrusion into victim organizations to date, the persistent attempts, and expansion in scope is cause for definite concern. XENOTIME has successfully compromised several oil and gas environments which demonstrates its ability to do so in other verticals. Specifically, XENOTIME remains one of only four threats (along with ELECTRUM, Sandworm, and the entities responsible for Stuxnet) to execute a deliberate disruptive or destructive attack.
XENOTIME is the only known entity to specifically target safety instrumented systems (SIS) for disruptive or destructive purposes. Electric utility environments are significantly different from oil and gas operations in several aspects, but electric operations still have safety and protection equipment that could be targeted with similar tradecraft. XENOTIME expressing consistent, direct interest in electric utility operations is a cause for deep concern given this adversary’s willingness to compromise process safety – and thus integrity – to fulfill its mission.
XENOTIME’s expansion to another industry vertical is emblematic of an increasingly hostile industrial threat landscape. Most observed XENOTIME activity focuses on initial information gathering and access operations necessary for follow-on ICS intrusion operations. As seen in long-running state-sponsored intrusions into US, UK, and other electric infrastructure, entities are increasingly interested in the fundamentals of ICS operations and displaying all the hallmarks associated with information and access acquisition necessary to conduct future attacks. While Dragos sees no evidence at this time indicating that XENOTIME (or any other activity group, such as ELECTRUM or ALLANITE) is capable of executing a prolonged disruptive or destructive event on electric utility operations, observed activity strongly signals adversary interest in meeting the prerequisites for doing so.”
Multiple ICS (Industrial Control Sectors) sectors now face the XENOTIME threat; this means individual verticals – such as oil and gas, manufacturing, or electric – cannot ignore threats to other ICS entities because they are not specifically targeted.
The Dragos researchers have termed this threat proliferation as the world’s most dangerous cyberthreat since an event in 2017 where Xenotime had caused a serious operational outage at a crucial site in the Middle East.
The fact that concerns cybersecurity experts the most is that this hacking attack was a malware that chose to target the facility safety processes (SIS – safety instrumentation system).
For example, when temperatures in a reactor increase to an unsafe level, an SIS will automatically start a cooling process or immediately close a valve to prevent a safety accident. The SIS safety stems are both hardware and software that combine to protect facilities from life threatening accidents.
At this point, no one is sure who is behind Xenotime. Russia has been connected to one of the critical infrastructure attacks in the Ukraine. That attack was viewed to be the first hacker related power grid outage.
This is a “Cause for Concern” post that was published by Dragos on June 14, 2019.
“While none of the electric utility targeting events has resulted in a known, successful intrusion into victim organizations to date, the persistent attempts, and expansion in scope is cause for definite concern. XENOTIME has successfully compromised several oil and gas environments which demonstrates its ability to do so in other verticals. Specifically, XENOTIME remains one of only four threats (along with ELECTRUM, Sandworm, and the entities responsible for Stuxnet) to execute a deliberate disruptive or destructive attack.
XENOTIME is the only known entity to specifically target safety instrumented systems (SIS) for disruptive or destructive purposes. Electric utility environments are significantly different from oil and gas operations in several aspects, but electric operations still have safety and protection equipment that could be targeted with similar tradecraft. XENOTIME expressing consistent, direct interest in electric utility operations is a cause for deep concern given this adversary’s willingness to compromise process safety – and thus integrity – to fulfill its mission.
XENOTIME’s expansion to another industry vertical is emblematic of an increasingly hostile industrial threat landscape. Most observed XENOTIME activity focuses on initial information gathering and access operations necessary for follow-on ICS intrusion operations. As seen in long-running state-sponsored intrusions into US, UK, and other electric infrastructure, entities are increasingly interested in the fundamentals of ICS operations and displaying all the hallmarks associated with information and access acquisition necessary to conduct future attacks. While Dragos sees no evidence at this time indicating that XENOTIME (or any other activity group, such as ELECTRUM or ALLANITE) is capable of executing a prolonged disruptive or destructive event on electric utility operations, observed activity strongly signals adversary interest in meeting the prerequisites for doing so.”
Guided Wave Radar Transmitters: Accurate and Reliable Level Measurement for the Widest Choice of Installation Options and Applications
Guided wave radar transmitters are widely used across different industries. These devices with their simple installation and trouble-free operations help industrial companies save time and money. They are ideal for a large number of process applications ranging from simple to complex.
How Do Guided Wave Radar Transmitters Work?
Guided wave radar transmitters rely on microwave pulses. Since microwaves are not affected by dust, pressure, temperature variations, and viscosity, this type of transmitter produces highly accurate results.
A low-energy microwave pulse is sent down a probe, and a part of it is reflected back when the pulse hits the process media. The liquid level is directly proportional to the time-domain reflectometry. The time when the pulse is launched and received back is measured to determine the distance from the surface of the media.
Types of Guided Wave Radar Level Transmitters
Guided wave radar level transmitters are available in different probe configurations. Selecting the right probe is important for successful implementation of the device. While manufacturers offer a range of guided wave radars, most are derived from the three basic probe configurations: single element, twin element, and coaxial.
Single element probe — The single element probe is the most widely used and least efficient device. The device is popular since it is more resistant to the coating of the liquid.
Twin element probe — The twin element probe is a good, general purpose probe that is generally used in long-range applications. They are ideal in situations where flexible probes are important for successful reading.
Coaxial probe — The coaxial probe configuration is the most efficient guided wave radar level transmitters. The probes are used in more challenging low-dielectric applications.
Benefits of Guided Wave Radar Level Transmitters
![]() |
Dielectric Constant and Reflectivity - Guided WaveRadar (GWR) (Courtesy of Schneider Electric Foxboro) |
Guided wave radar level transmitters provide a range of benefits in different applications. The concentration of the measuring signal is strong and clean. This is due to the narrow path of the signal propagation that reduces the chances of impact by stray signals due to obstacles or construction elements inside the tank.
Another benefit of guided wave radar level transmitters is that they are easy to install. No mounting holes are required to install the device. This results in cost savings for the organization. The waveguide can be formed to follow the tank’s contours or mounted at an angle.
The device is ideal in situations where an interface measurement is required. The measuring signals can penetrate the medium deeply, resulting in more accurate results. The waveguide technology is suitable for applications where the medium is subjected to heavy vapors, foam, and dust.
Guided wave instruments can detect changes in dielectric consents on the boundary of a property. The device can be configured to detect level at both the top and the bottom of a layer of emulsion.
Industrial Application of Guided Wave Radar
Guided wave radar level transmitters are increasingly being used in process industries. The sensors are used in situations that previously employed ultrasonic, hydrostatics, and capacitance. The accuracy specification of the basic model range is up to ±5mm, while the accuracy of the advanced models is up to ±2mm.
The device is generally used in industries to take level readings. The readings are used for local indication and visualization in control systems.
Moreover, guided wave radar level transmitters are also used for managing liquid inventory, determining safety limits, dry run protection, and leak detection. Other applications of guided wave radar level transmitters include communicating low limits to suppliers, automated ordering systems, and streamlining the logistics process.
Guided radar level measurement is also suitable for bulk solids. The surface type is not restricted to liquids since the reflected waves are guided easily through any medium. Foam formation and turbulent liquid surfaces and different angled surfaces (as is the case with bulk solids) don’t influence the accuracy of the reading.
Selection of Guided Wave Radar Level Transmitters
Selection of guided wave radar level transmitters should be based on the requirements of the task. Generally, the rigid single element probe configuration is ideal for angled installations for flowing liquids. The dual flexible wire probe is suitable for most other common applications.
A coaxial probe configuration is recommended for liquids that are cleaner with low dielectric constant and with turbulence on the product’s surface. This type of guided wave radar device is also recommended for installations where the probe is near the tank wall or other obstacles.
Make sure that the device can withstand the range of temperature within the tank. Most GWR devices are rated up to 850 deg F or 450 deg C. You should select a device with added signal strength since this will result in increased reliability and accuracy of the devices.
Guided wave radar level transmitter with dynamic vapor compensation is recommended where a high level of accuracy is required under a high-pressure environment. The measurement taken from the device can compensate for changes in vapor dielectric, which results in improved accuracy.
Other factors that should be considered include mounting and proximity. Single probe configuration can be installed almost anywhere. But the single probe configuration can only to apply to specific situations.
Lastly, the probe length of the device should be of the right length. The length should be according to the measurement rate. This is an important consideration as it can help in ensuring accurate reading with minimum chances of an error.
Guided wave radar level transmitters can also be used with an agitator. However, certain things must be considered prior to use the device. The probe must be prevented from contacting the agitator blades. Make sure that you confirm the ability of the probe to withstand the force inside the medium. This is important since turbulent on the surface may decrease the accuracy of the measurement. You can install the device in a bypass chamber or stilling well for an agitated tank.
For more information on guided wave level transmitters, contact Swanson Flo by calling 800-288-7926 or by visiting their web site at https://swansonflo.com.
Posted by
Swanson Flo
Labels:
Foxboro,
Guided wave radar transmitter,
Illinois,
Indiana,
Iowa,
level control,
Michigan,
Minnesota,
Montana,
Nebraska,
North Dakota,
South Dakota,
Wisconsin,
Wyoming
Hazardous Area Classifications in the USA
![]() |
Understanding Hazardous Area classifications is critical. |
Hazardous areas refer to locations with a possible risk of explosion or fire due to dangerous atmosphere. The hazards can be associated with flammable vapors or gases, ignitable fibers, and combustible dusts.
Different hazardous area classifications exist in the North America and Europe. Generally, the National Electric Code (NEC) classifications govern hazardous areas in the US. While in Europe, hazardous area classification has been specified by the International Electrotechnical Commission (IEC).
CLASS
|
NATURE
OF HAZARDOUS MATERIAL
|
CLASS I
|
Hazardous area due the presence of flammable vapors or gases
in sufficient quantities to produce ignitable mixtures and cause
an explosion.
Examples include
natural gas and liquified petroleum.
|
CLASS II
|
Hazardous area due the presence of conductive or combustible
dusts in sufficient quantities to produce ignitable mixtures
and cause an explosion.
Examples include
aluminum and magnesium powders.
|
CLASS III
|
Hazardous area due the presence of flammable fibers
or other flying debris that collect around lighting fixtures,
machinery, and other areas in sufficient quantities to produce
ignitable mixtures and cause an explosion.
Examples include
sawdust and flyings
|
Division groups hazardous areas based on the chances of an explosion due to the presence of flammable materials in the area.
DIVISION
|
LIKELIHOOD
OF HAZARDOUS MATERIAL
|
DIVISION 1
|
Areas where there is
a high chance of an explosion due to hazardous material that is
present periodically, intermittently, or continuously under normal
operation.
|
DIVISION 2
|
Areas where there is
a low chance of an explosion under normal operation.
|
Group categorizes areas based on the type of flammable or ignitable materials in the environment. As per NEC guidelines, Groups A to D classify gasses while Groups E to G classify dust and flying debris.
GROUP
|
TYPE
OF HAZARDOUS MATERIAL IN THE AREA
|
GROUP A
|
Acetylene.
|
GROUP B
|
Area contains flammable gas, liquid, or liquid produced vapor with
any of the following characteristics:
Examples include hydrogen, ethylene oxide, acrolein, propylene
oxide.
|
GROUP C
|
Area contains flammable gas, liquid, or liquid produced vapor with
any of the following characteristics:
Examples include carbon monoxide, hydrogen sulphide, ether,
cyclopropane, morphline, acetaldehyde, isoprene, and ethylene.
|
GROUP D
|
Area contains flammable gas, liquid, or liquid produced vapor with
any of the following characteristics:
Examples include ammonia, gasoline, butane, benzene, hexane,
ethanol, methane, methanol, natural gas, propane, naphtha, and
vinyl chloride.
|
GROUP E
|
Area contains metal dusts such as magnesium, aluminum, chromium,
bronze, titanium, zinc, and other combustible dusts whose
abrasiveness, size, and conductivity present a hazard.
|
GROUP F
|
Area contains
carbonaceous dusts such as charcoal, coal black, carbon black,
coke dusts and others that present an explosion hazard.
|
GROUP G
|
Area contains combustible dusts not classified in Groups E and F.
Examples include
starch, grain, flour, wood, plastic, sugar, and chemicals.
|
NOTE: This post serves only as a guide to acquaint the reader with hazardous area classifications in the USA. It is imperative to discuss your instrumentation, valve, or process equipment requirement with a qualified applications expert prior to installing any electrical device inside of any hazardous area.
800-288-7926
Posted by
Swanson Flo
Labels:
Hazardous Area Classification,
Illinois,
Indiana,
Iowa,
Michigan,
Minnesota,
Montana,
Nebraska,
North Dakota,
process control,
South Dakota,
Valves,
Wisconsin,
Wyoming
Flowserve Valtek Control Valve Packing Adjustments
For more information about Flowserve Valtek valves, contact Swanson Flo by calling 800-288-7926 or by visiting https://swansonflo.com.
Posted by
Swanson Flo
Labels:
Control Valve,
Flowserve,
Illinois,
Indiana,
Iowa,
maintenance,
Michigan,
Minnesota,
Montana,
Nebraska,
North Dakota,
packing,
South Dakota,
Valtek,
Wisconsin,
Wyoming
Wireless Networking in Industrial Plants
Using a wireless system can result in an efficient supply of networking resources to field devices. The system facilitates an effective exchange of data between the host server and the field devices in the industrial setting.
Only a few industry-grade wireless field sensors have been offered so far in the year 2019. The reason for this is mainly a lack of information regarding its benefits. Once the cost-saving aspects of wireless networking become known in the industrial setting, it will likely spur the demand in the market and lead to an influx of innovative wireless devices for different field applications.
Benefits of Wireless Networking Systems in the Industrial Setting Explored
Wireless technologies offer great value over wired solutions. A reduction in cost is just one of the many benefits of switching to the wireless networking system. There are many benefits, including enhanced management of legacy systems that were previously not possible with a wired networking connection.Here is an overview of some of the value-added benefits of adopting wireless networking in industrial plants.
Reduced Installation Costs
Savings in installation costs is the key benefit of a wireless networking system. The cost of installing a wireless solution is significantly lower as compared to its wired counterpart.Installing a wireless network requires less planning. Extensive surveys are not required to route the wires to control rooms. This reduced installation cost is the main reason industrial setups should consider going wireless instead of having a wired networking system.
Improved Information Accuracy
Adopting wireless networking also results in improved accuracy of information. The wireless system is not prone to interferences. As a result, the system ensures consistent and timely transfer of information from one node to another.Enhanced Flexibility
Enhanced flexibility is another reason for deploying wireless networking solutions in an industrial setting. Additional points can be awarded easily in an incremental manner. The wireless system can also integrate with legacy systems without any issues.Operational Efficiencies
Migrating to wireless networking can help in improving operational efficiencies as well. Plant managers can troubleshoot and diagnose issues more easily. The system facilitates predictive maintenance by allowing the monitoring of remote assets.Human Safety
Another critical factor that should influence the decision to migrate to wireless networking is the human safety factor. Wireless technologies allow safer operations, reducing exposure to harmful environments. For instance, a wireless system can be used in taking a reading and adjusting valves without having to go to the problematic area to take measurements.Efficient Information Transfer
Another advantage is that the time required to reach a device is reduced. This results in a more efficient transfer of information between network segments that are geographically separated. The industry wireless networking standards use IP addresses to allow remote access to data from field devices.With wireless networking systems, readings can be taken more frequently that can help in early detection and reduction of possible incidents.
Wireless Networking Standards for Industrial Plants
The ISO100 standards committee has introduced a whole set of new standards for wireless communication in industries. The first standards include the ISA100.11 that pertains to processing data transfer while fulfilling limited control needs in the industries.![]() |
Hybrid architecture using WirelessHART mesh networking coupled with ultra-efficient BLE Instrument Area Networks. Image courtesy of Foxboro Schneider Electric. |
Technical Basis
ISA100.11a is based on IEEE 802.15.4:2006 standard, similar to WirelessHART with 15 to 16 channels in the ISM band 2.4GHz range. However, the former can be used for a wider networking application in the industrial sector such as peer-to-peer messaging and network segmentation.Distinct Hopping Patterns
Each segment in the network may use a distinct hopping pattern, unlike the WirelessHART. Moreover, the network segment has a dedicated time slot that results in the formation of large networks with overlapping segments.Mesh Networking
Another important point to note is that the ISA1001.11a wireless networking standard for industrial process makes use of mesh networking, which is similar to WirelessHART. However, the standard also allows devices at the network’s edge to not route information to different devices. This results in increased security that prevents unauthorized access to networks.While not being technically different, the details of the two standards set them apart. However, the IS100.12 is already in development, and it will reduce the divergence in specifications between WirelessHART and ISA100.11a.
Challenges in Adopting Industrial Wireless Networking
Industrial wireless communication technology is a work in progress. A lot of work is required to address specific technical challenges for adopting the networking solution. Some of the challenges include evaluation and communication of the wireless technologies that are available for industrial concerns.Another challenge in the adoption of wireless technology is solving the issues of latency or time synchronization. This is important to ensure the reliability of data transferred in the industrial setting.
Based on the challenges identified, here are three key suggestions for implementing wireless technology in the industrial setting.
- Create a science-based methodology for measuring the performance of wireless communication
- Create guidelines for the deployment of wireless networking in an industrial environment
- Address issues of latency in systems with high-reliability aspects with error rates less than 10 percent
Key Takeaway
Wireless networking is an enabling technology that can result in improved operational efficiency in the industrial systems. The technology can improve control and safety and lead to enhanced cost savings.Adoption of the wireless networking system creates huge potential for increased operational efficiencies. The system can reduce installation cost, enable enhanced monitoring, reduce risks, and improve profitability.
For more information on industrial wireless networking, contact Swanson Flo by calling 800-288-7926 or by visiting https://swansonflo.com.
Posted by
Swanson Flo
Labels:
field instruments,
Illinois,
Indiana,
Iowa,
Michigan,
Minnesota,
Montana,
Nebraska,
networking,
North Dakota,
process control,
South Dakota,
wireless,
wireless instrumentation,
Wisconsin,
Wyoming
Swanson Flo Has You Covered
Founded in 1960, Swanson Flo has long maintained our position as an industry leader in process automation with unmatched project success leveraging industry preferred products and services. Our mission is to provide innovative process control solutions for engineers, managers and maintenance professionals through quality equipment and experienced application engineering.
Swanson Flo
https://swansonflo.com
800-288-7926
Posted by
Swanson Flo
Labels:
Control Valves,
Illinois,
Indiana,
instrumentation,
Iowa,
Michigan,
Minnesota,
Montana,
Nebraska,
North Dakota,
process equipment,
South Dakota,
valve automation,
Wisconsin,
Wyoming
An Excellent Industrial Valve Glossary for the New Engineer, Technician, Maintenance Person or Buyer
Here's a great resource (courtesy of Jordan Valve) for the new process engineer, plant maintenance person, industrial valve buyer, or service technician. This document is called "A Glossary of 864 Valve Terms". This may be the most comprehensive valve glossary we've ever seen. We hope you find it useful.
Attend the 2019 BioFuels Automation University Ethanol Maintenance Classes
The 2019 BioFuels Automation University schedule is now released. Interested parties should review the course itineraries and plan to attend.
BioFuels Automation University provides Best Practice Certification courses designed to enable participants to learn directly from some of the industry’s top technical professionals and gain valuable hands-on training to best utilize the technology driving your facilities.
A strong combination of concepts and best practice Hands-on Training – this course really delivers for insight and troubleshooting skills for instrumentation and valve technologies. BioFuels Automation University experts stand ready to help define your needs and craft a customized program.
Two Sessions available in 2019:
Day Two: Valves - Automated On/Off Valves, Valve Monitors, Control Valves, Positioners, Communication Protocols, Shop Tools - Hands On
Fee: $1,350 per participant. Fee includes lodging and meals. Payment information required to complete registration.
Location: BioFuels Automation University Training Center, 151 Cheshire Lane, North Plymouth, Minnesota
BioFuels Automation University provides Best Practice Certification courses designed to enable participants to learn directly from some of the industry’s top technical professionals and gain valuable hands-on training to best utilize the technology driving your facilities.
Ethanol Maintenance 101
A strong combination of concepts and best practice Hands-on Training – this course really delivers for insight and troubleshooting skills for instrumentation and valve technologies. BioFuels Automation University experts stand ready to help define your needs and craft a customized program.
- Jun 20 - 21, 8:00 AM
- Oct 24 - 25, 8:00 AM
Day Two: Valves - Automated On/Off Valves, Valve Monitors, Control Valves, Positioners, Communication Protocols, Shop Tools - Hands On
Fee: $1,350 per participant. Fee includes lodging and meals. Payment information required to complete registration.
Location: BioFuels Automation University Training Center, 151 Cheshire Lane, North Plymouth, Minnesota
Ethanol Maintenance 201
All devices and technologies from 101 will covered in-depth at the master technician level. Course structure is 80% hands-on and centered around your specific plant needs. To maximize the impact of this course, extensive application challenges as well as Q&A sessions are conducted. BioFuels Automation University experts stand ready to help define your needs and craft a customized program.
This class will take you through an analysis of the complete control loop, providing you with a deeper understanding of the relationship between the three segments of a control loop. Sensing Element, PID Controller, Final Control Element, C (control) DCS, I and V.
Two Sessions available in 2019:
Topics covered: Loop Configurations, Controller PID Tuning: Theory and Practical Application Instruments, Advanced Valves
Fee: $2,250 per participant. Fee includes lodging and meals. Payment information required to complete registration.
Location: BioFuels Automation University Training Center, 151 Cheshire Lane, North Plymouth, Minnesota.
This class will take you through an analysis of the complete control loop, providing you with a deeper understanding of the relationship between the three segments of a control loop. Sensing Element, PID Controller, Final Control Element, C (control) DCS, I and V.
- July 25 - 26, 8:00 AM
- Dec 05 - 06, 8:00 AM
Topics covered: Loop Configurations, Controller PID Tuning: Theory and Practical Application Instruments, Advanced Valves
Fee: $2,250 per participant. Fee includes lodging and meals. Payment information required to complete registration.
Location: BioFuels Automation University Training Center, 151 Cheshire Lane, North Plymouth, Minnesota.
The Flowserve Valtek MaxFlo 4 Eccentric Rotary Plug Control Valve
The Flowserve Valtek MaxFlo 4 control valve is a high performance eccentric rotary plug valve designed for the process industry. It features a large capacity, standard hardened trim and superior shaft blow-out protection. This valve is available in sizes 1 through 12 inches, ASME Class 150, 300 and 600 as well as DIN PN 10, PN16, PN 25, PN40 and PN63.
An optional ISA 75.08.01 or DIN EN 558 series 1 long-pattern body makes this valve an easy drop-in replacement for a globe control valve.
Posted by
Swanson Flo
Labels:
Control Valve,
Illinois,
Indiana,
Iowa,
MaxFlo 4,
Michigan,
Minnesota,
Montana,
Nebraska,
North Dakota,
South Dakota,
Valtek,
Wisconsin,
Wyoming
Schneider Electric Foxboro Pressure Transmitter Models 05S/10S/50S
Available in absolute pressure, differential pressure and gauge pressure, the new Schneider Electric Foxboro Models 05S/10S/50S pressure transmitters are designed to make your process more profitable by giving you the opportunity to select your transmitter at the best ratio of performance/price for your application.
Innovative FoxCal™ technology, accuracy expressed as a percentage of reading, 400:1 turndown, Safety SIL2 certification, are some of the exceptional features in the 05S/10S/50S family.
For more information, contact:
Swanson Flo
https://swansonflo.com
800-288-7926
Posted by
Swanson Flo
Labels:
05S,
10S,
50S,
Foxboro,
Illinois,
Indiana,
Iowa,
Michigan,
Minnesota,
Montana,
Nebraska,
North Dakota,
pressure transmitter,
Schneider Electric,
South Dakota,
Wisconsin,
Wyoming
Types of Electrical Connectors Used for Hamilton Process Analytics Sensors


K8 connectors are typically used on pH / ORP sensors which lack temperature compensation. These connectors have a two pole design comprised of the center core and outer metallic threaded connection.

S7 & S8 – S7 and S8 connectors are typically found on sensors which no temperature compensation. They are the same basic design however S8 connectors have PG13.5 mounting threads, while S7 connectors do not. These connectors are recessed thus care must be taken to avoid moisture getting trapped which could lead to a short circuit.

M12 - Metallic threaded M12 connectors are found on Dissolved Oxygen Sensors and Cell Density products. M12 adapters have either 4 or 8 poles hidden within the socket. Since the poles are recessed avoid getting moisture inside the connection.

T82 – The T82 connector is sometimes known as a D4 connector. It uses a twist lock design to secure the cable to the sensor. These connectors are less common.

connections on Memosens connectors.
For more information on Hamilton ProcessAnalytics contact Swanson Flo.
https://swansonflo.com
800-288-7926
Posted by
Swanson Flo
Labels:
connectors,
Hamilton Process Analytics,
Illinois,
Indiana,
Iowa,
Michigan,
Minnesota,
Montana,
Nebraska,
North Dakota,
process analytics,
South Dakota,
Wisconsin,
Wyoming
Changing the Trim on the Jordan / LowFlow Mark 708 Series Control Valve
The LowFlow Mark 708 is a very popular and accurate control available for fractional flow services: whether for pilot plant installations, test stands, R & D facilities or for specialized processes such as dosing, injection and venting applications. This video demonstrates how to change the trim on the Jordan / LowFlow Mark 708 Series Control Valve.
Swanson Flo
https://swansonflo.com
800-288-7926
A Visual Understanding of Steam Induced Water Hammer
When improperly drained of condensate in a high pressure steam main fills with condensate and completely surrounds the steam, an implosion takes place causing devastating water hammer.
Draining condensate and keeping it away from the steam by using proper steam trapping equipment will prevent this from happening.
The following video, courtesy of TLV, dramatically demonstrates the principle behind water hammer and its potentially devastating effects.
Swanson Flo
https://swansonflo.com
800-288-7926
Posted by
Swanson Flo
Labels:
condensate,
Illinois,
Indiana,
Iowa,
Michigan,
Minnesota,
Montana,
Nebraska,
North Dakota,
South Dakota,
steam,
TLV,
water hammer,
Wisconsin,
Wyoming
Flowserve Valves - Kammer Control Valves

FLOWSERVE Kämmer pneumatic actuators are widely known for their versatile diaphragm design, easy installation and simplified maintenance. When compared to other manufacturers’ diaphragm actuator designs, Kämmer actuators have much higher thrust capabilities, feature a very compact design and are lighter in weight. They also feature a field reversible design that requires no additional parts.
Download the Kammer Control Valve Product Profile Here
Posted by
Swanson Flo
Labels:
Control Valves,
Flowserve,
Illinois,
Indiana,
Iowa,
Kammer,
Michigan,
Minnesota,
Montana,
Nebraska,
North Dakota,
South Dakota,
Valves,
Wisconsin,
Wyoming
Mounting the Logix 3800 Digital Positioner on the Valtek Mark One Linear Control Valve
Compatible with linear and rotary valves and actuators, the Logix 3800 digital positioner offers industry-leading embedded measurement, data reduction and diagnostic functionalities. It features powerful diagnostics that identify field problems and expedite corrective actions to ensure reduced return-to-operation times.
The Valtek Mark One globe control valve offers superior performance in liquid and gaseous services, while also permitting easy, fast and inexpensive maintenance.
This video details how to mount the Logix 3800 positioner on the Mark One valve.
For more information about Flowserve valve and valve automation products, contact Swanson Flo by calling 800-288-7926 or visit their website at https://swansonflo.com.
Posted by
Swanson Flo
Labels:
Control Valve,
Illinois,
Indiana,
Iowa,
Logix,
Michigan,
Minnesota,
Montana,
Nebraska,
North Dakota,
positioner,
South Dakota,
Valtek,
Wisconsin,
Wyoming
Subscribe to:
Posts (Atom)