Download the Flowserve Cavitation document here.
According to Wikipedia, "Cavitation is the formation of vapor cavities in a liquid, small liquid-free zones ("bubbles" or "voids"), that are the consequence of forces acting upon the liquid. It usually occurs when a liquid is subjected to rapid changes of pressure that cause the formation of cavities in the liquid where the pressure is relatively low. When subjected to higher pressure, the voids implode and can generate an intense shock wave."
Cavitation presents serious concerns to engineers and specifiers of control valves. Understanding ways to mitigate cavitation is important. Flowserve has put together this excellent document on understanding cavitation and offers solutions on reducing or eliminating its effects.
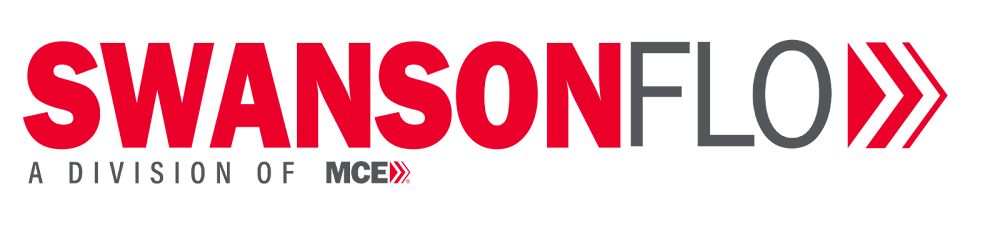
The Swanson Flo Blog is dedicated to provide educational and new product information on process control instrumentation, control valves, and valve automation. For more information on these products, visit SwansonFlo.com or call 800-288-7926.
Understanding Cavitation in Valves
Posted by
Swanson Flo
Labels:
cavitation,
Flowserve,
Illinois,
Indiana,
Iowa,
Michigan,
Minnesota,
Montana,
Nebraska,
North Dakota,
South Dakota,
Wisconsin,
Wyoming
Comprehensive Steam in Place (SIP) Whitepaper Available

What are the rules and common piping practices employed to ensure that steam sterilization occurs on time without fail? What are SIP temperature validation alarms, or faults? Why do they occur? How does thermostatic steam trap operation affect the occurrence of temperature validation faults? What new technologies are available to mitigate common SIP problems? Specific answers to these questions will be covered in this white paper.
Get your copy of the "Steam in Place (SIP)" whitepaper here.
Table of Contents:
- What Is SIP?
- Fundamentals Of Process Equipment Steam Sterilization
- Sanitary Balanced Port Thermostatic Steam Trap Operation
- Validation Temperature Alarms Caused By High Subcooling Trap Operation
- Problem Remediation
- What Is A Sanitary Subcooled Condenser?
- The SSC Series Explained Special SIP Applications For Large Vessels
- Special SIP Applications: Conventional SIP Process Design For Larger Vessels
- Special SIP Applications: Problems With Conventionally Designed SIP Drains For Large Vessels
- Special SIP Applications: New Solution For SIP Design For Larger Vessels
Swanson Flo
800-288-7926
Posted by
Swanson Flo
Labels:
Illinois,
Indiana,
Iowa,
Michigan,
Minnesota,
Montana,
Nebraska,
North Dakota,
SIP,
South Dakota,
Steam in Place,
Steriflow,
Wisconsin,
Wyoming
Differential Pressure Gauge Designed for Harsh Environments
![]() |
Ashcroft F5509/F6509 |
The F5509/F6509 differential gauges are ideal where safe and reliable pressure measurement is essential:
Process Control Markets:
- Refineries
- Chemical and Petrochemical Plants
- Water and Wastewater Pressure Control
- Mining and Metals
- Filter, Level and Flow Measurement
For more information about any Ashcroft product, contact Swanson Flo by calling 800-288-7926 or by visiting https://swansonflo.com.
Posted by
Swanson Flo
Labels:
Ashcroft,
differential pressure gauge,
Illinois,
Indiana,
Iowa,
Michigan,
Minnesota,
Montana,
Nebraska,
North Dakota,
South Dakota,
Wisconsin,
Wyoming
Full Service Valve Automation
From simple pneumatically or electrically actuated valves, to fully automated critical valve systems, Swanson Flo delivers tested, certified, and extremely reliable product every time. Actuated valve assemblies precisely engineered for the best fit, highest performance, and optimal life.
With decades of combined experience and knowledge, Swanson Flo technicians match state-of-art components with best-in-class manufacturers and deliver carefully crafted valve packages.
Swanson Flo customers always receive the highest quality and best value possible. Their strong reputation was built upon:
- The largest, most comprehensive facility in the Midwest.
- In-house capabilities for all electric, pneumatic and electro-hydraulic actuators.
- Experienced design engineering and fabrication.
- Support for assembly of all valve, actuator, monitor and positioner technologies.
- Complete solution for testing and serialization.
800-288-7926
Posted by
Swanson Flo
Labels:
electric,
Illinois,
Indiana,
Iowa,
Michigan,
Minnesota,
Montana,
Nebraska,
North Dakota,
pneumatic,
South Dakota,
valve actuation,
valve automation,
Wisconsin,
Wyoming
The Basics of Control Valve Actuators
![]() |
Control Valve (Flowserve Valtek) |
Control valve actuators control fluid in a pipe by varying the orifice size through which the fluid flows. Control valves contain two major components: the valve body and the valve actuator. The valve body provides the fluid connections and a movable restrictor comprised of a valve stem and plug that is in contact with the fluid that varies the flow. The valve actuator is the component that physically moves the restrictor to vary the fluid flow.
The video below introduces the viewer to basic control valve operation concepts and the basic types of actuators.
Posted by
Swanson Flo
Labels:
Cashco,
Control Valve,
Flowserve,
Illinois,
Indiana,
Iowa,
Michigan,
Minnesota,
Montana,
Nebraska,
North Dakota,
South Dakota,
Valtek,
Wisconsin,
Wyoming
Worcester Controls Valve and Actuator Product Catalog
Here is a new Product Catalog for Flowserve Worcester Control industrial ball valves, pneumatic actuators and electric actuators, courtesy of Swanson Flo. These include standard flanged ball valves, ANSI and DIN specifications in reduced and full bore, three-piece valves for cryogenic, high pressure, steam, diverter or sampling duty, high integrity valves, multi-way designs, modulating controls or customized solutions.
Posted by
Swanson Flo
Labels:
actuator,
ball valve,
cryogenic valve,
https://swansonflo.com,
Illinois,
Indiana,
Iowa,
Michigan,
Minnesota,
Montana,
Nebraska,
North Dakota,
South Dakota,
Wisconsin,
Wyoming
Subscribe to:
Posts (Atom)